The opening or the Tynes Bay Waste Treatment Facility brought to a conclusion possibly the most complex and critical project ever undertaken by the Bermuda Government. Until this time, all of Bermuda's waste (garbage) was going to landfills, most notably the Marsh Folly site in Pembroke. In the early 1980's, with 80,000 tonnes of domestic and commercial waste being generated annually, the Island's only landfill site was nearing capacity and producing unacceptable problems for local residents. The Government at this time decided to replace landfill as a method for disposal of combustible waste with the provision of a municipal "waste-to-energy" mass burn incinerator.
In 1987 the Government engaged Von Roll Ltd. of Switzerland to design, procure and install the incinerator's mechanical and electrical plant. After a delay of three years due to environmental concerns, approval was given to restart the project. At the start of 1991 the Ministry project team faced the challenges of coordinating the design and the considerable task of bringing together the multi-national workforce to construct the $70 million facility on this small, isolated, mid-Atlantic island.
The primary role of incineration in Bermuda's waste management plan is to reduce the volume of combustible waste by up to 90% to minimize the reliance on land filling as the primary means of solid waste disposal. A secondary and important function of the facility is to extract energy from the gasses to produce electricity for the facility and to export to the local power company (BELCO) grid.
In addition to the and valuable energy savings, there is an indirect benefit to Bermuda's economy by reducing diesel fuel imports and hence foreign currency requirements.
The facility has two streams each capable of incinerating 6 tonnes per hour. Each stream is designed for continuous operation. Incoming waste is inspected and weighed prior to discharge into the refuse bunker located in the tipping hall. The waste is mixed to provide a reasonably homogeneous material before it goes into the furnace. The temperature of combustion is controlled by the volume of air and the rate of feed through the combustion chamber. The grate in the combustion chamber both turns and tumbles the waste to facilitate complete burnout.
The hot flue gases from the combustion process are cooled at various locations by passing them over banks of boiler tubes containing water. The steam produced is superheated to 400 degrees Celsius and at a pressure of 45 bar. This steam is fed to a steam turbine coupled to an alternator. The electricity produced by the turbo-alternator is fed to the facilities distribution system and in turn is inter-connected with BELCO to enable energy to be either imported from, or exported to, the public supply system. Each stream of the plant has the capacity to produce in excess of 2.5 MW of electricity, approaching 5% of the island's average need.
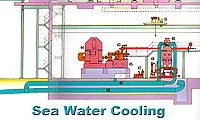
After driving the turbine, the steam is condensed by sea water and passed back into the boiler system via a de-aerator to ensure water is returned to the boiler free of gases. If the turbine is shut down, the combustion process will continue by diverting the steam from the boilers to separate dump condensers.
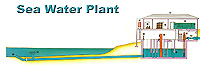
The sea water used for condensing the steam is drawn through the pumping station located on North Shore Road. Band screens, located in the for bay of the pumping station, prevent coarse sand particles, seaweed and other sea life from entering the pipes. The sea water is returned to the ocean at approximately 10 degrees above the ambient. This warmed water is dispersed into 8 m depth of ocean via a 35 m outfall through a diffuser angled at 10 degrees to the seabed.
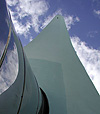
The combustion gases, after having given up their heat in the boilers, are cleaned by passing through the electrostatic precipitators which remove in excess or 99% or particulate matter. From there, fans emit the gases to atmosphere through chimney flues at a height of 91 meters above sea level, 75 m above the surrounding ground level, a height which ensures good dispersion.
Monitoring equipment continuously measures temperature, oxygen, carbon monoxide, sulphur dioxide, hydrogen chloride and opacity to establish that emissions remain within permitted limits.
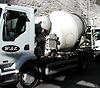
Ash that drops off the furnace grates (bottom ash) and the particulates removed by the electrostatic precipitators (fly ash) are transported to the quench tank. The combined wet ash is then conveyed to the ash bunker for storage. Ash handling equipment in the Ash Plant is used to process the ash. It is graded by passing over a 100mm screen, and ferrous material is removed with a magnetic separator. the ash is weighed and the moisture content determined prior to mixing with cement to form ash concrete to a strength of approximately 10 N/mm2 .
This ash concrete is formed into 1 metre cube blocks, each weighing about 2 tonnes, which are used for shore protection and land reclamation at the Airport Waste Management Facility. |